Уголь и кокс: черная полоса? (Часть 2) 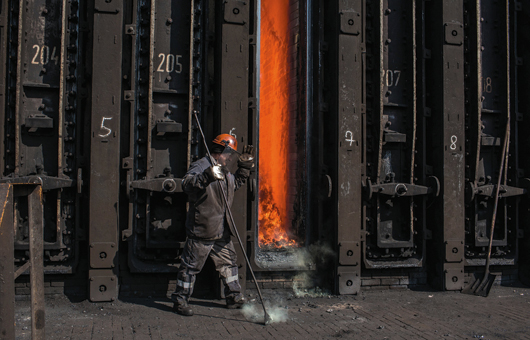
В отличие от рынка коксующегося угля, о котором мы писали в первой части этой статьи, российский рынок продукта его переработки – металлургического кокса – в меньшей степени зависит от мировой конъюнктуры. Фактически все определяется возможностью экспортной отгрузки из РФ этого ценного металлургического сырья.
Отметим, что вывоз металлургического кокса на дальние расстояния был и остается затруднительным чисто технологически. Перевалка и транспортировка резко ухудшает (дробит) фракционный состав этого непрочного продукта. Для него также желательны меры защиты от влаги, возгорания и т.д. Поэтому объемы мировой торговли коксом традиционно на два порядка меньше, чем аналогичные показатели для металлургических углей. А сравнительно небольшие поставки кокса преимущественно идут ближайшим соседям.
Россия при всей нестабильности экономики (и дефиците долларов) вынуждена следовать общемировым тенденциям. Поэтому объемы экспорта кокса существенно уступают как объемам его производства, так и внутрироссийского потребления (рис. 1).
В начале 2016 года крайне выгодный (при низком курсе рубля) экспорт российского кокса продолжил свое снижение. По данным ФТС РФ, в январе он упал на 29,2% в годовом сравнении, до 92,5 тыс. т. При этом производство кокса в РФ в указанном месяце снизилось всего лишь на 6,8%, до 2,072 млн т. Это означает, что доля российского потребления кокса приблизилась к рекордным 98% от общих объемов его производства в стране.
Причина, скорее, в проблемах с логистикой и экспортом, нежели в опережающем внутреннем спросе на это сырье. Хотя вывод этот не является очевидным. Так что рассмотрим его несколько подробнее.
Около 95% произведенного в России металлургического кокса традиционно применяется в классическом доменном процессе выпуска чугуна. Поэтому должна быть четкая взаимосвязь этих производств и рынков (рис. 2).
Отметим, что в последние годы производство чугуна в РФ растет опережающими темпами. К примеру, по данным Росстата, в 2015 году оно увеличилось на 4,48%, в то время как производство стали – снизилось на 1,5%. Основная причина – в многочисленных санкциях против импорта из РФ различной стальной продукции, но в отсутствии таковых против поставок чугуна.
Даже США – инициатор многих российских проблем – за 2015 год увеличили закупки российского чугуна в 1,5 раза.
И в итоге купили около половины общих объемов этого экспорта из РФ, который за год вырос на 22,5%, до 5,34 млн т.
Но объемы выпуска кокса в РФ, как и его видимого потребления, уже многие годы практически не растут. Причина этого технологическая, причем весьма прогрессивная.
Пара десятилетий модернизации черной металлургии РФ привела к заметной экономии сырья в производстве. Один из важнейших показателей доменного процесса – расход кокса на тонну выплавляемого российского чугуна – заметно снизился (рис. 3).
Фактически в отрасли произошла компенсация роста выпуска чугуна более эффективным использованием металлургического кокса. Спрос российских металлургов на это сырье практически не изменился.
В общей сложности в РФ находится в эксплуатации до 60 коксовых батарей схожего типа мощностью от 0,40 млн до 1,15 млн т кокса в год. Но их суммарная мощность (около 45 млн т кокса в год) полностью не используется, что позволяет оперативно вести работы по ремонту и модернизации.
Отметим, что средний срок эксплуатации коксовых батарей составляет 30–35 лет, т.е. «запас прочности» в отрасли при грамотной эксплуатации оборудования сохранится надолго.
ЧерМК «Северстали», например, недавно завершил крупный ремонт коксовой батареи №2, начавшийся в 2007 году. Неспешность его была связана с полной перекладкой простенков всех 65 камер коксования.
При этом ремонт проходил в условиях действующего производства и фактически – только в осенне-зимние месяцы. А сейчас «Северсталь» инвестирует порядка 6 млрд рублей в реконструкцию коксовой батареи №4 ЧерМК с плановым сроком ее окончания в 2019 году. В среднем за последние годы распределение мощностей по выпуску кокса в РФ близко к реальной (внутренней) потребности наших основных металлургических комбинатов (рис. 4).
Лидером (с учетом мощностей «Алтай-кокса») является группа НЛМК, существенно расширившая в последние годы мощности своего доменного производства. Аутсайдерами – отдаленные от потребителей «Москокс» (группа «Мечел») и «Губахинский кокс» (группа ОМК).
Отметим, что на территориях меткомбинатов расположено более 80% коксохимических производств, что существенно упрощает процесс транспортировки этого сырья к доменным печам, минимизирует потери и складские запасы и т.п.
Падающий вывоз кокса на экспорт (о чем мы писали в начале статьи) погоды на рынке почти не делает. Рост поставок российского кокса на Украину также остается ограниченным (в 2015 году – 719 тыс. т). Украинские коксохимы, в частности Авдеевский КХЗ, лоббируют ввод пошлин на импорт с целью обеспечить работу своих коксовых батарей. Кстати, с 1 апреля в РФ вырастет и экспортная пошлина на металлургический кокс – c $2,5 до $3,5 за т.
А прочие внешние отгрузки кокса российским потребителям (предприятиям цветной металлургии, литейным производствам в машиностроении и т.п.) продолжают оставаться незначительными и составляют ныне менее 4% потребления в черной металлургии РФ. Однако они, как и экспорт, несколько запутывают ситуацию с российскими ценами на металлургический кокс (рис. 5).
Цены внутреннего рынка на кокс, по данным Росстата, весьма точно следуют именно за экспортными ценами и курсом рубля ЦБ РФ. При этом по мировым меркам цены эти весьма высоки: соотношение стоимости российс-кого кокса к ценам собственного коксующегося угля стабильно держится на уровне 3,5–4. Это заметно выше, чем в Китае и других «металлургических странах», но легко объяснимо.
Основная часть нашего кокса продается внутри горно-металлургических холдингов по сравнительно невысоким трансфертным ценам, выпадая из официальной статистики. А прочим, т.е. «чужим», потребителям предлагается платить за него сполна.
Подводя итоги, можно сказать, что производство кокса в нашей стране строго сбалансировано с внутренним спросом черной металлургии на него. Избытков практически нет. Пожалуй, это и к лучшему, учитывая степень экологической вредности и опасности данного производства.
Собственники, естественно, не согласны с такой оценкой, но порой им все же приходится признавать обратное. Так, в начале марта «Мечел-Кокс» частично остановил свое коксохимическое производство после многочисленных жалоб жителей Челябинска на смог и повышенного внимания со стороны властей.
Схожая ситуация бывает и в других металлургических городах. Группа «Евраз» в 2015 году уже снизила продажи кокса на 15%, а сейчас сообщила об инвестициях в 175 млн рублей, которые будут направлены на сокращение выбросов коксохимического производства «Евраз НТМК».
В кризис это весьма хорошая новость...
|