Автосталь – новая, старая и не только... (Часть 2) 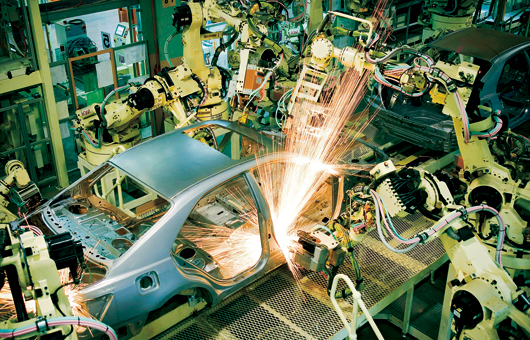
В первой – июльской – части этой статьи мы описали главную тенденцию мировой автомобильной промышленности в последние десятилетия. Она – в явном повышении экологичности и экономичности массовых автомобилей. В частности, путем снижения их массы (при сохранении прочности) за счет расширения доли новых конструкционных материалов, таких как пластики, композиты, алюминиевые сплавы. А также благодаря применению новых высокопрочных марок стали и технологий переработки.
Теперь обратимся к российской практике взаимодействия автостроителей и металлургов.
Начнем с «Северстали», которая около двух десятилетий проявляла особый интерес к поставкам своей высокопередельной продукции автопрому. Еще в 2003 году «Северсталь» сообщала, что поставила 36% всего металла, использованного на АвтоВАЗе, 69% – на ЗИЛе, 61% – на ГАЗе и 82% – на УАЗе. Совокупно доля «Северстали» на российском рынке автостали достигала в те годы 50%.
В 2004 году «Северсталь» за $280 млн приобрела в США крупного (до 4 млн т проката в год) производителя автомобильного листа – металлургический завод Rouge Steel в Детройте. Предприятие было основным поставщиком стали на соседний автозавод корпорации Ford, причем для ускорения отгрузок обходилось без общего забора! И естественно, Rouge Steel располагала современными и конкурентоспособными производствами автомобильного металлопроката, технологии которых в некоторой степени позже внедрялись на российских производствах «Северстали».
В результате 10 лет назад российская компания могла похвастать ежегодными экспортными отгрузками около 25–35 тыс. т готовой стальной продукции автомобилестроителям в США (Ford), Италию (Fiat), Испанию (Bamesa), Китай (Ssang Young), Южную Корею (Hyundai) и Узбекистан (Daewoo).
Интерес «Северстали» к рынку автосталей был неслучаен. Вплоть до 2012 года ситуация с российским производством автомобилей выглядела достаточно динамично и перспективно (рис. 1).
Аномальный спад показателей автопрома РФ в 2009–2010 годах никого особо не смутил. Глобальный ипотечно-финансовый кризис схожим образом задел большинство стран мира. Важнее стало другое: судя по статистике, российские автозаводы неплохо научились справляться с растущим потоком импорта автомобилей в Россию. Если в 2008 году он впервые обогнал по объемам внутреннее производство, то через пару лет уже отставал от него вдвое-втрое.
Однако «успехи» борьбы нашего автопрома с импортом (активно поддерживаемые властями РФ) являются относительными. Многие годы на российских автозаводах неуклонно росла сборка иномарок. Стабилизация произошла только сейчас, причем на весьма высоком уровне – с долей около 75% рынка (рис. 2).
Более того, исходя из статистики первого полугодия 2017 года, «наступление» на авторынок иномарок российской сборки вновь ускорилось. По данным аналитической компании «АСМ-холдинг», производство легковых автомобилей в РФ за январь–июнь 2017 года увеличилось на 19,4%, до 642,95 тыс. штук. При этом выпуск продукции иностранных брендов вырос на 21,5%, до 480,3 тыс. штук.
Отметим, что доля легковых автомобилей в продукции отечественного автопрома близка к 95%, а ее распределение по маркам (брендам производителей) плавно, но неуклонно изменяется не в пользу отечественных разработок. К примеру, доля производства группы АвтоВАЗ (ныне в составе Renault-Nissan) на российском рынке за 10 лет снизилась с 70 до 33% (по мнению наших министерств) или даже ниже 23% (по мнению независимых аналитиков). Соответствующее распределение выпуска автомобилей по заводам и маркам в прошлом году приведено на рис. 3.
Вопрос локализации этих многочисленных производств, т.е. перехода на российские конструкционные материалы и комплектующие, остается открытым. Напомним, что в 2005 году правительство РФ ввело (а в 2011 году – продлило до 2020 года) режим промышленной сборки, в рамках которого иностранцы должны были достигнуть высокого уровня локализации (до 60%), получив взамен возможность беспошлинно ввозить комплектующие.
По данным Минпромторга, средний уровень локализации иномарок в России сейчас близок к 50%. Прежде всего это произошло за счет простых комплектующих – деталей интерьера, фар, аккумуляторов, колесных дисков, топливных баков и т.д. Лучше других отчитывается о достигнутом уровне локализации (до 70%) АвтоВАЗ. И это естественно, поскольку не так давно он составлял 100%. С приходом в Тольятти концерна Renault-Nissan и освоением сборки многих иномарок ситуация изменилась. В то же время с 2014 года здесь освоено производство двигателей и коробок передач по лицензии Renault-Nissan. А модели Renault Logan, Sandero и Duster получили также и широкий ряд штампованных в России элементов кузова.
Пониже уровень локализации на российских заводах Hyundai, Volkswagen, Ford и Nissan, где этот показатель составляет 40–50%. Еще ниже он при сборке Peugeot и Citroen, Toyota Camry, а вседорожники Mitsubishi Outlander и Pajero Sport изготавливаются в России с локализацией лишь на уровне около 20%. Кстати, именно этот низкий уровень и слабые перспективы стали причиной свертывания производств GM в Петербурге (выпуск Сhevrolet, Opel Astra и т.д.).
Отразился автомобильный спад спроса после 2013 года и на российских производителях комплектующих. Закрытие завода GM и сокращение выпуска Ford привели к закрытию производства сидений Johnson Controls в Ленобласти (сохранив площадку в Тольятти). Там же свернула производство Magna, переориентировавшаяся на выпуск метизов в Калугу. Японская Unipress приостановила проект штамповки кузовных деталей в парке поставщиков Nissan в Санкт-Петербурге.
ММК, запустивший в 2010 году в этом регионе завод штампованных компонентов («Интеркос-IV»), не обнаружил спроса и фактически свернул производство в 2016–2017 годах.
Тем не менее, по мнению Минэкономразвития и Минпромторга, в 2016 году 61% произведенных в России легковых автомобилей относятся к моделям с высоким уровнем локализации (50% и выше), спроектированным на базе автомобильных платформ глобальных OEM. Основные объемы производства приходятся на следующие массовые и современные платформы: B0 группы Renault-Nissan, KP2 группы Hyundai и PQ25 группы Volkswagen.
Отметим, что эти позитивные выводы наших чиновников во многом базируются на оптимистичных заявлениях автомобильных компаний, а они сейчас не слишком объективны. Причина – в огромном интересе к сохранению соглашений по промсборке, т.е. беспошлинном ввозе комплектующих в Россию.
Уточним статистику нашего автопрома в части импортозамещения по более четким показателям – фактическому потреблению черных металлов (проката, труб и т.п.) за последние годы (рис. 4).
По данным ж/д перевозок, охватывающих более 95% поставок металла, тенденция вырисовывается очевидная. За последнее десятилетие доля российского металла, используемого в производстве российских автомобилей (включая грузовики и автобусы), сократилась вдвое, до уровня около 700 кг на автомобиль. А с учетом отходов металлообработки в автопроме реально отечественного металла в готовом автомобиле оказывается ниже полутонны. Прочий металл – это та самая импортная комплектация (металлом, метизами, автокомпонентами), доля которой в последние годы практически не снижается.
При этом основными потребителями отечественных черных металлов (проката, труб и т.п.) в автопроме РФ остаются его традиционные потребители – ВАЗ, КамАЗ, ГАЗ и УАЗ (табл. 1).
Отметим, что эта «большая четверка» (с филиалами) в 2006–2016 годах обеспечивала около 58% всего потребления металлов в российском автопроме, а в текущем году увеличила свою долю до 74%.
При этом среди 15 крупнейших автопотребителей отечественной стальной продукции оказалось лишь 2 представителя «новой волны» – метизных производств, ориентированных, в частности, на поставки для промсборки иномарок.
Первое – ООО «Северсталь-Гонварри-Калуга» – совместное российско-испанское предприятие, основанное в 2009 году и оснащенное, в частности, современным оборудованием фирмы Fagor, которое «способно обеспечить высочайшее качество выпускаемой продукции».
По данным компании, с момента основания она переработала около 400 тыс. т металла, т.е. около 50 тыс. т в год. По нашим оценкам, эта цифра несколько ниже, но главное другое. Использование производственных мощностей «Северсталь-Гонварри-Калуга» в среднем находится на уровне 30% и ниже. Помимо основных поставок (автопрому) эта компания активно ищет покупателей метизной продукции в других отраслях российского машиностроения.
Среди заметных покупателей нашего металла также находятся российские подразделения компании Mefro Wheels GmbH (ООО «Мефро Уилз Руссиа Завод Заинск» и ООО «Мефро Уилз Руссиа Завод Тольятти»). Германская Mefro Wheels является мировым поставщиком стальных колесных дисков для легковых и грузовых автомобилей. Помимо Германии и России она имеет крупные предприятия во Франции, Турции и Китае. В нашей стране компания активно работает с 2011 года после покупки колесных производств у КамАЗа и АвтоВАЗа. Инвестиции в их модернизацию составили около 3,9 млрд рублей, а выпуск дисков сейчас приблизился к 1 млн шт. в год. Mefro Wheels сообщает об успехах на российском рынке и своих поставках на производства Ford, GM, BMW, Renault, КамАЗ, АвтоВАЗ, Man, Volvo и других, т.е. на большинство автозаводов РФ. Однако потребности метизных производств Mefro Wheels в РФ в стальном прокате (с учетом массы дисков) не слишком велики и составляют сейчас около 30 тыс. т в год. А на роль основных его поставщиков выдвигаются ЧерМК и ИТЗ «Северстали».
Отметим также (на основании данных табл. 1) резкое – с 34,5 до 9,5% – сокращение поставок российских черных металлов прочим представителям российского автопрома. Это (помимо остановки ряда заводов) указывает на процесс концентрации наших автомобильных производств, включая СМЦ и метизные заводы по выпуску деталей и компонентов.
Рассмотрим динамику отгрузок российских черных металлов автопрому по основным поставщикам (рис. 5).
Во-первых, отметим в месячной динамике ее крайнюю нестабильность по объемам. Предсказуемым спрос нашего автопрома на металлы никак не назовешь, что крайне отличает его от мировых конкурентов. Кроме того, есть немало вопросов к автомобильным компаниям РФ в части своевременной оплаты металлопродукции, постоянной борьбы за «эксклюзивное» снижение цен и т.д.
Оптимизм «Северстали» и НЛМК, ориентировавшихся на развитие производства современной автостали, в некоторой степени угас после труднейших переговоров с автозаводами по ценам качественного стального проката. Череповецкому меткомбинату, например, в 2011 году не удалось согласовать цены автомобильного плоского стального проката с АвтоВАЗом. Поставки, составлявшие некогда 10–25 тыс. т в месяц, упали практически до нуля и не восстановились до сих пор. В июле 2017 года ж/д отгрузки в Тольятти из Череповца для всех видов черных металлов составили всего лишь 922 т, а за полугодие – 7709 т. При этом «Северсталь» сообщила о поставках за 6 месяцев 2017 года прочим автопроизводителям РФ и СНГ более 220 тыс. т металлопродукции, что на 14% больше, чем годом ранее.
Долю «Северстали» (как и долю НЛМК и прочих производителей) во многом перехватил Магнитогорский меткомбинат (ММК). По итогам 2016 года ММК сообщил о поставках предприятиям автомобильной отрасли 473 тыс. т металлопродукции, что на 12,6% превышает аналогичный показатель предыдущего года. Отдельно отмечен рост на 34,5% поставок ММК иностранным автопроизводителям, локализующим свои сборочные мощности в России. Увы, всего лишь до незначительного объема 26,9 тыс. т. Однако общая динамика поставок магнитогорской стали автопрому РФ в последние годы выглядит весьма убедительно. ММК явно обыгрывает конкурентов и усиливает свои позиции на этом рынке (рис. 6).
Впрочем, Магнитка выигрывает за счет поставок недорогого и классического автомобильного листа без каких-либо инноваций, подобных тем, что мы описывали в первой части этой статьи. При этом поставки российского стального проката на сборочные производства иномарок в РФ остаются совсем незначительными.
Директор по связям с общественностью Мария Мальцева из «Хендэ Мотор Мануфактуринг Рус» (ХММР Hyundai) отмечала пару лет назад, что «мы ежегодно выпускаем более 200 тыс. автомобилей, и для нас важно иметь надежных поставщиков автокомпонентов. При этом главными критериями в выборе поставщиков для нас являются соответствующее международным стандартам качество автокомпонентов, конкурентная с точки зрения глобального рынка цена и своевременные поставки в необходимом объеме.
К сожалению, на сегодняшний день не все российские поставщики отвечают этим критериям». И по-прежнему локализация производства Hyundai Solaris, Kia Rio и т.п. обходится практически без российского металла. Даже самые бюджетные, без современной оцинковки, южнокорейские модели автомобилей «родом из России» предпочитают импортный металл (чаще от метзавода Hyundai Hysco), который перерабатывается метизным производством Hyundai Hysco Rus рядом с Санкт-Петербургом.
Калужское предприятие «Фольксваген Груп Рус» сообщает о наибольшем уровне локализации производства в РФ за счет инвестиций объемом Ђ1,75 млрд. В 2015 году оно запустило завод по производству двигателей, а в 2016 году открыло новый кузовной цех площадью 12 тыс. кв. м, включающий и линию гальванического цинкования. Однако автомобили марок Volkswagen и Skoda сходят с его конвейеров также с минимумом российского металла.
В первом полугодии текущего года, по данным аналитической компании «АСМ-холдинг», выпуск российских автобрендов вырос только на 13,8% – при росте сборки иномарок в РФ на 21,5% и явном торможении темпов локализации. В условиях антироссийских санкций инвестиции в нашу страну идут крайне неохотно.
Тем временем приближаются 2018–2020-е годы и пересмотр соглашений о промсборке иностранных автомобилей в России. Теперь одним росчерком пера чиновники правительства РФ могут прекратить беспошлинный ввоз автокомплектующих – в пользу «Лада-Калина» и прочих российских автоплатформ. А могут, как уже бывало, продлить нашу дружбу с германским, французским и южнокорейским автопромом.
И вновь все решат не экономические соображения, а чистая политика. К чему нам в России в последние годы не привыкать...
|