Железо для «железного» потребителя 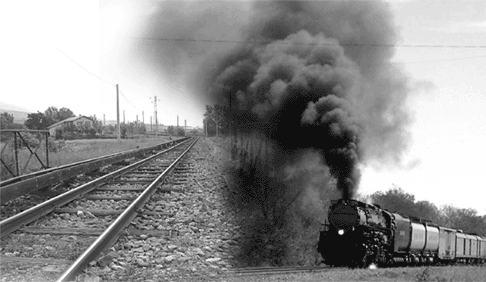
Железные дороги традиционно являются заметным потребителем продукции черной металлургии во всем мире. Продукция железнодорожного назначения условно делится на ту, что предназначена непосредственно для прокладки дорог – это рельсы, подкладки, клеммные и закладные болты, арматура шпал и прочее оборудование строения пути; и на ту, что идет на конструирование подвижного состава – элементы корпусов вагонов, локомотивов, цистерн и т. п., включая колеса, оси, бандажи и т. д. И если прямой потребитель первой группы продукции – сами железнодорожники, то второй – предприятия тяжелого машиностроения (локомотиво- и вагоностроительные и ремонтные и т.п). Вторая группа не в полной мере охватывается статистикой, однако в целом мировое потребление металла железнодорожной отраслью оценивается в 10 млн. т в год, что составляет около 1,2% от объема производства мировой черной металлургии.
Специфика российской географии (отсутствие удобных водных путей с Запада на Восток), и обширная территория задали свои традиции транспортной индустрии. Железные дороги по сети протяженностью около 160 тыс. км. осуществляют более 80% российских грузовых перевозок, а расширение доли авто- и авиаперевозок идет медленнее, чем в развитых и малых странах. И такая ситуация сохранится на многие десятилетия. Потребление металла железнодорожным транспортом (МПС) в России существенно превосходит мировой уровень и составляет в последние годы 1,5-1,6 млн т (без учета подвижного состава). Это около 2,5% всего российского производства и около 7% внутреннего потребления.
Основную металлопродукцию для железных дорог производит в России всего лишь несколько крупных производителей, для которых этот ассортимент является лишь одним из направлений их деятельности. Шире выбор производителей в секторе вспомогательных крепежных метизов ж/д путей: подкладок, болтов и т.д. Соответствующая структура потребления металла приведена ниже,
а основные производители продукции для железнодорожников на Рис.4.
Около 40% потребляемого металла составляет рельсовый прокат для ж/д путей. Ежегодно в России обновляется около 15 тыс. км верхнего строения пути, в т.ч. 4 тыс. км укладываются на новых рельсах.
Основными производителями рельсов для МПС (основного и монопольного их заказчика) являются Нижнетагильский металлургический комбинат (НТМК) и Кузнецкий металлургический комбинат (КМК), в последние годы входящие в состав «Евразхолдинга». Технологически НТМК имеет лучшие возможности для производства рельсов, однако их доля в общем объеме производства проката на комбинате только 10%. На КМК в 2002 году она составила 31% (увеличившись с прошлого года на 3%). Однако комбинат является технологически отсталым, находится в затяжном кризисе и 30 мая прошедшего года был признан банкротом. Его реорганизация с созданием ООО «Рельсы КМК» ситуацию улучшила незначительно. В итоге на аукционе 28 января 2003 года «Рельсы КМК» проданы ООО «Спецмаш-МТ» за 793,95 млн руб. Новому хозяину производства придется приложить немало сил по его обновлению, в т.ч. удовлетворению требований к качеству рельсов со стороны МПС.
Ссылаясь на недостаточное качество российских рельсов, МПС в период 1997-2001 года до 15% необходимого рельсового проката закупало в Японии (и даже в Канаде). Некоторые из этих закупок проведены по фактической цене до 900$/тонну, в то время как соответствующие закупки в России (под диктатом МПС) проводились по ценам на уровне 2,5-3,0 тыс.руб./т. Любопытные подробности части этих и других расходов МПС приведены в бюллетене Счетной палаты РФ №1(37) 2001 года. Отметим, правда, что необоснованный импорт рельсов на сумму $150 млн явился одной из претензий Правительства РФ к МПС, в конце концов вызвавших отставку министра Аксененко.
На долю КМК и НТМК в поставках для МПС приходилось в последние годы около 650 тыс. т рельсов, при том что текущая его потребность составляет в среднем 0,8-0,9 млн т рельсов в год.
Другие потребители (подъездные пути предприятий, трамвайные пути и т.д.) потребляли менее 20% рельсов. Так что основную «погоду» на этом рынке, безусловно, делало и делает МПС. Напомним, что в советские годы министерство закупало около 2 млн. тонн проката и лоббировало строительство производственных мощностей в металлургии еще на 2 млн тонн (основная часть – рельсы). В 2002 году МПС активизировала свою техническую политику в части качества рельсового проката. Надеемся, что это реальные меры именно для снижения импорта, а не для показухи.
Так, например, в марте 2002 года на КМК закончилась работа Межведомственной рельсовой комиссии (легендарная организация, которой более 100 лет). Рельсовая комиссия (с участием всех нужных сторон и специалистов) отметила, что металлурги КМК и НТМК успешно освоили новый ГОСТ на рельсы и в 1999-2001 годах значительно улучшили качество продукции. Особо отмечено освоение производства рельсов из электростали на КМК и ввод дифференцированных цен на рельсы разного качества. Кстати, 16 декабря 2002 года сообщено, что рельсы типа Р-65 для высокоскоростных магистралей и рельсы высокой низкотемпературной надёжности производства КМК стали лауреатами национального конкурса «Российская Марка», проводимого РСПП (серебряный знак качества). КМК сообщил, что в 2002 году МПС отгружено 38 тыс. т высокоскоростных рельсов и 210 тыс. т низкотемпературных, что превышает показатели 2000 г. соответственно в 4 и 37 раз.
Однако в реальности не все так гладко. Перевод всей железнодорожной продукции НТМК на современный уровень качества эксперты от МПС оценивают в $150 млн затрат, а для КМК – в $300 млн затрат. Металлурги надеются обойтись инвестициями вдвое-втрое ниже. Но и в прошлом году силовым решением сверху, и разгружая НТМК, «Евразхолдинг» увеличивает загрузку кризисного производства КМК заказами МПС до максимально возможного уровня. Из производства и людей выжимается буквально все...
НТМК благополучнее и технологически подготовлен много лучше. Начиная с 80-х годов почти непрерывно ведется значительная реконструкция его производства. Ныне металл для рельсов варят в кислородном конвертере, разливают его через МНЛЗ. Комбинат владеет технологиями вакуумирования, микролегирования, объемной закалки, изотермической выдержки, шлифования рельсов и т.д, т.е. способен выпускать много лучшую продукцию, чем КМК. Показателем для НТМК является растущий поток заказов из стран – бывших республик СССР, Ирака, Канады (RONSCO Technologies) и т.д. Однако повышение качества рельсов для российского МПС далеко не всегда компенсируется их ценой. Прогрессивные технологии в производстве часто не задействуются, а серьезных средств давления на заказчика-монополиста у металлургических комбинатов нет.
Главное сейчас в рельсовом производстве России – организационные вопросы, вплоть до политических. Напомним, что кемеровский губернатор Аман Тулеев обещал «закрыть собою рельсы на родном Кузнецком металлургическом комбинате». Комбинат градообразующий и без вмешательства властей не может быть ни закрыт, ни реорганизован. А реформирование монополиста в лице МПС – вообще вопрос государственного уровня и не предмет этой статьи...
Другим важнейшим для МПС производством является выпуск железнодорожных колес. В России их основные производители – Выксунский металлургический завод (ВМЗ) и НТМК. ВМЗ является крупнейшим производителем данного вида продукции в Европе, а на российском рынке колес его доля оставляет порядка 63%.
В середине 2002 года МПС заключило с Выксунским МЗ соглашение о поставках железнодорожных колес сроком на 8 лет на сумму порядка $800 млн, предусматривающее поставки размером в 40 тыс. штук колес ежемесячно, начиная с 2003 года. В настоящее время доля колес в структуре производства предприятия составляет порядка 20%. В 2002 году их производство возросло на 16% по сравнению с 2001 годом, до 549,1 тыс. штук (рис. 5)
Колесное производство НТМК менее значительно. Кроме поставок МПС, Нижнетагильский комбинат рассматривает вопрос кооперации в производстве колес с германской фирмой «Бохумер Ферайн» и планирует выпуск колес по требованиям RONSCO Technologies для североамериканских дорог.
Отметим также, что общая же доля НТМК на российском рынке производства черного металла для нужд железных дорог достигает 50%. Большую часть элементов верхнего строения пути (подкладки, болты, шурупы, костыли, противоугоны, шайбы и др.) выпускают ЧСПЗ, МКЗ, МММЗ, ОСПАЗ и Уральский завод металлоконструкций. Многие эти метизы являются высокотехнологичной продукцией высокой прочности, но ввиду низких закупочных цен МПС дефицитны.
Реконструкция и ремонт путей в России худо или бедно все же ведется. Хронический «дефицит» средств МПС в течение последних лет компенсирует значительным сворачиванием строительства подвижного состава железных дорог.
В настоящее время в России находятся в эксплуатации около 1,1 млн. грузовых вагонов различных модификаций. Из них 550 тыс. принадлежит МПС (из них 324 тыс. полувагонов и 105 тыс. вагонов-цистерн, на ходу лишь 320 тыс.), около 40 тыс. находятся у операторов, остальные – в собственности предприятий. Что касается железнодорожных цистерн, то в настоящее время их рабочий парк в России составляет примерно 180 тыс. единиц, из них 98 тыс. – у частных собственников.
Так что вопрос обновления вагонного парка все больше решается вне МПС, на прямых договорах с Уралвагонзаводом или Демидовским заводом, заметными потребителями черного металла.
На конец 2002 года перевалил за отметку 50% дефицит локомотивов, срок службы многих из которых будет исчерпан к 2005 году. По договору с МПС, в 2003 году Коломенский завод поставит 26 тепловозов. Планируется ряд договоров МПС и с другими поставщиками локомотивов и пассажирских вагонов. Так что можно ожидать роста потребления металла в этом году со стороны Тверского вагоностроительного и Воронежского вагоноремонтного заводов.
Прогноз
Все плюсы и минусы этого сектора рынка продиктованы монопольным положением его главного заказчика – МПС России. Железнодорожное хозяйство страны обречено на стабильность в течение многих десятилетий и одновременно – на реформирование в ближайшие годы. Существующее состояние дел накапливает как его проблемы, так и недовольство всех потребителей железнодорожных транспортных услуг.
Износ путевого хозяйства имеет четкие пределы. Далее следует растущая аварийность, и ситуация напоминает кризис ЖКХ страны. Только вот авария Транссиба, например, ведет, по мнению властей, к более серьезным последствиям, чем «замерзание» очередного российского города. Слишком велики экономические потери. Так что при любом сценарии реформирования стабильность потребления металла путевым хозяйством гарантирована. Это прочно устоявшаяся ниша с давно известными всем и друг другу партнерами. Попал в нее – получил гарантию сбыта на годы.
Чуть живее ситуация на рынке спецметизов крепежа, где есть ниша для малых производств, готовых рискнуть инвестициями ради стабильной, но невысокой прибыли. Непредсказуем сейчас рынок железнодорожного строительства. В него входят конструкции железнодорожных мостов, депо и ангары для вагонов, эстакады, различные несущие конструкции для силовых кабелей и т. п. Некоторые из них стандартные, большинство же изготавливается по единичным заказам. Денежное выражение этого рынка огромно и до конца реформы непредсказуемо. Например, стоимость моста с материка на Сахалин, сооружение которого планировалось начать в 2001-2002 годах и который так и не был реализован из-за отсутствия у МПС денег, составляла ориентировочно 10-14 млрд долларов. Отметим впервые в российской новой истории открытие в 2002 году частной железной дороги в Коми группой «СУАЛ». Масштабных проектов, включая новые железные дороги – немеряено, но большинство их сейчас заморожено. А в части подвижного состава, например, для экспортных перевозчиков рынок, наоборот, «оттаял».
Итоговый баланс – стабильный застой. А кто хочет жить на рынке металлов поспокойнее, должен с железной дорогой дружить. Хоть будет без сюрпризов и в курсе всех перемен!
Статья была опубликована 20 февраля 2003 года в журнале "Металлургический бюллетень" (№ 4).
|